Imagine you are talking to a team of engineers, who are pulling their hair out about a design for leg prosthetics. They picked aluminum because it is a super light and affordable material. But it seems to be too soft and sensitive for the purpose: customers complain about corrosion and scratches.
“Have you thought about using anodized aluminum?”, you ask the engineers. “Anodizing will make the leg prosthetics much more durable and even a climb in the mountains or a swim in the sea will do nothing to the super-strong anodized aluminum surface!”
What is aluminum anodizing (Type II)?
Anodizing is an electrochemical process, which thickens the naturally formed oxide layer on the aluminum surface. Growing the oxide layer from nanometers to microns in thickness, anodizing can change the properties of the aluminum product, resulting in higher corrosion resistance, coloring ability, and a consistent appearance.
By changing the properties of the surface, anodizing makes aluminum more versatile for products and applications. Coming back to the example of a leg prosthesis, anodizing makes aluminum a suitable material for prosthetics because it changes the properties of the aluminum surface.
There are several types of anodizing: chromic acid anodizing (Type I), sulfuric acid anodizing (Type II), and hard anodizing (Type III). The most common method is sulfuric acid anodizing (SAA), which is used in 70% of all anodized products. If you want to more learn about what aluminum anodizing is, read this blog post.
How to anodize – the full anodizing process
The anodizing process consists of three phases: pre-treatment, anodizing, and post-treatment. In total, the anodizing process has seven process steps (excluding rinsing), which you can see in the image below. The first three steps cleaning, etching, and desmutting happen in the pre-treatment phase. Anodizing is a step in itself, while coloring and sealing are part of the post-treatment.
An important but often overlooked step in the anodizing process is rinsing. Rinsing means immersing the aluminum pieces in a tank with clear water. The rinsing should happen between each step of the anodizing process to make sure the surface is ready for the next process step. As this practice is crucial to avoiding anodizing defects, you can learn all about it in the e-learning course “Aluminum Anodizing – Rinsing.”
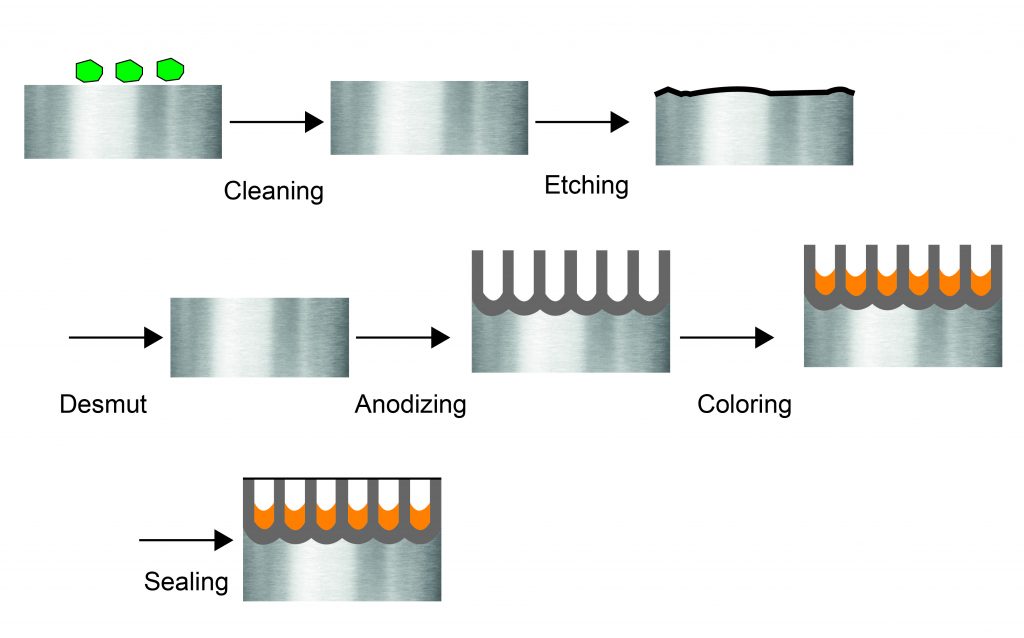
Step 1: Cleaning
To prepare the aluminum surface for anodizing, the metal needs to be cleaned. For cleaning, a mild non-corrosive solution is best to remove machining residuals, grease, and even fingerprints.
Here is an expert tip: make sure to wear white cotton gloves when handling the aluminum throughout the whole anodizing process. This way you make sure not to leave grease on the aluminum surface. Also, it makes it super easy to detect dirt or dust particles as your white gloves make stains visible. If you would like to learn more about all the pitfalls to avoid when racking the aluminum pieces, check out the Anodizing Masterclass module “Aluminum Anodizing – Handling and Racking.”
Step 2: Etching
Etching involves removing die lines and other surface defects from the extrusion or other semi-fabrication manufacturing processes. It also removes the naturally formed oxide layer. The most common etching process is alkaline. In this process step, the surface becomes smooth and has an even appearance, if processed correctly.
Step 3: Desmutting
During the etching process, some alloys will form black smut on their surface from the alloying elements which do not dissolve in the alkaline process. Therefore, the last step of the pre-treatment process is desmutting, which removes the smut and prepares the aluminum surface for the acidic anodic solution.
Step 4: Anodizing
During Type Il anodizing, the aluminum is submerged in a tank with an electrolyte consisting of sulfuric acid and water. In the tank, an electrical current builds the anodic film on the aluminum surface, thereby forming a thicker artificial oxide layer with a porous structure.
What happens in the anodizing tank changes the properties of the final product. Therefore, to ensure the anodized parts match the product requirements, it is essential to discuss the desired properties with the supplier and create specifications for the product.
Step 5: Coloring
At this stage in the anodizing process, the aluminum surface has a porous oxide structure. The porous structure is like a sponge, which makes it great for absorbing coloring particles. Most coloring methods work by filling these pores with “coloring” material.
Step 6: Sealing
Finally, the aluminum is sealed, which closes the porous structure to create the highest protection of the final coating. This step ensures a long-lasting surface finish that will keep the aluminum protected for many years—if it is done correctly.
In contrast, poor sealing will leave the aluminum surface open to chemical and physical damage. This is because the porous aluminum oxide structure is highly adsorbent, which means that water or aggressive substances can enter the pores, diminishing the corrosion protection and fading the colors.
Various sealing methods are available and selecting the correct one depends on the environment of the final product. It is therefore important to discuss the application of the sealing step with the supplier to determine the right sealing method.
The secret for better-than-best anodizing
Great anodizing results do not depend on the anodizer’s competence alone. Open communication between the anodizer and the customer is key to creating anodized surfaces with exactly the properties needed— and without color variations or poor sealing.
When receiving aluminum parts, the customer should discuss with the anodizer the coloring and post-treatment specifications in order to determine what the right coloring and sealing methods should be. In addition, the customer should provide the anodizer with information about the alloy and metallurgical history of the aluminum part, as well as the environment in which the final product will be used.
Improve your anodizing results
Now you should have an understanding of how to anodize aluminum. If you found this article helpful sign up for our newsletter to receive free knowledge about aluminum anodizing. For more in-depth knowledge, check out the Anodizing Masterclass, an e-learning course with more than 10 hours of video lectures to learn everything about anodizing. You can also ask for consulting or a customized workshop on any topic of your choice. I consult both anodizers as well as OEMs, engineers, designers, and anyone else who is working with anodized aluminum parts.
If you liked the blog post, you might also like our blog post about 5 Anodizing Defects That Happen in the Handling and Pretreatment Steps.
If you are working with anodized parts, we have a practical checklist for you! This checklist helps you to get exactly the anodized parts you want for your product. Simply fill out the form and receive the checklist.
Are you working in an anodizing shop or your company is thinking to set up an in-house anodizing line? Then grab our to-do list for anodizers. Simply fill out the form and receive the to-do list.