One of the greatest benefits of anodizing is the formation of a structural porous aluminum oxide. In this “sponge”, you can create a beautifully colored surface that will not chip or peel nor compromise the recyclability of the aluminum product. When it comes to the coloring step, you typically have four different coloring processes for anodized aluminum:
a) Adsorption/Dying
b) Electrolytic
c) Integral
d) Interference
Adsorption and Electrolytic are the major coloring processes, Integral coloring is on its way out and Interference is gaining popularity.
The 4 different coloring processes in aluminum anodizing
We will go through each color process in detail, but here are the most important differences: In Adsorption, Electrolytic and Interference coloring anodizing is done as a separate step before the coloring whereas Integral coloring is done during anodizing. The most commonly used coloring process for outdoor exposure is Electrolytic coloring due to its high light fastness. This light fastness depends on the metal deposition in the pores. The Interference coloring has also a superior light fastness and can create more colors than Electrolytic coloring.
The drawing below shows the four different types of coloring, a) Adsorption, b) Integral c) Electrolytic, and d) Interference.
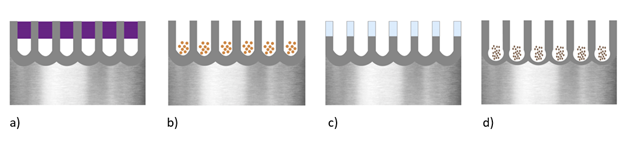
Adsorption
When Adsorption is used the dying solution can be organic or inorganic. The porous oxide layer is immersed into the solution directly after anodizing. The dye will flow into the open pores filling the outer part of the oxide layer (see drawing a). The final sealing of the layer is done to enclose the dye inside the pores.
When using an organic solution almost all colors are possible, however, there are some uncertainties about the lightfastness (fading) as some of the colors have a lower resistance to UV exposure. It should also be noted that some of the black colors among others are containing chrome (VI) which is banned and not an environmental solution to use.
Electrolytic
The Electrolytic coloring method (see drawing b) consists in immersing the anodized part in an acidic solution containing metal salts and then normally applying an alternating current to precipitate the metal ions. This process is also called the two-step coloring process.
The metal salts used can be cobalt, nickel, and tin. Tin is the most common one, giving different coloring tones from bronze to black shades. The color obtained by this method is also very dependent on the thickness of the oxide layer and the alloying elements found in the material. This coloring process is more UV resistant than the adsorption coloring process. However, this coloring method does not give you the full coloring spectrum as it is limited to bronze and black shades when using tin.
Integral
Integral coloring (see drawing c), also called one-step coloring, is performed in the anodizing electrolyte, which can consist of organic acids such as oxalic acid, sulphosalicylic acid, and others. Here the color of the coating is dependent on the thickness of the oxide layer, varying from light yellow to black. These coatings have a very high wear resistance and hardness.
Also, variation in alloys is used to exhibit differences in colors of the oxide layer. This type of coloring is normally not used due to the high price of process cost.
Interference
Modification of the barrier layer or the structure of the pore in the bottom, as seen in drawing d) can expand the color spectrum. Interference coloring is one of these coloring processes where an intermediate step between anodizing and coloring is introduced. This process step could be for example a phosphoric acid treatment to enlarge the pores. The colors obtained ranged from blue to green and pink/red. This coloring process creates greater UV resistance and allows for more color variation.
Watch the free video “Anodized Aluminum Coloring” at AnodizingSchool to learn more about the coloring process of anodized aluminum.
When to choose which process
So, which is the right coloring process for your anodized aluminum product? First, consider the exposure to UV light. For example, window frames have high exposure to UV light. For this type of product Electrolytic and Interference coloring is most suitable. But maybe you have a very specific idea for the coloring and the product is barely exposed to light, as it is for example the case for hi-fi products? In this case, it makes sense to use dye (Adsorption) as it is cheaper.
If you liked this blog post, you might also like “How to Anodize Aluminum – Type II Anodizing for Beginners” to learn the basics of anodizing.
Level up: Get more help getting perfectly colored anodized aluminum
Are you working with anodized products? Or do you work an Anodizing Line yourself?
Either way, we’ve got some tools to help you.
For OEM’s, product managers, designers, etc.
Click here to get the checklist that helps you get perfectly anodized aluminum products from your supplier (if you’re a OEM, product manager, designer, etc.)
For Anodizers
Grab our list of 4 things to do today to increase the revenue of your Anodizing Line if you’re an anodizer by clicking here.