Does your company develop and sell aluminum products that have to withstand harsh environments? For example, suspension systems for motorbikes or rotor blades for helicopters flying in the desert? I have helped many companies creating amazing, durable products by understanding the hard anodizing finish.
Hard anodizing is an amazing surface treatment that turns a too-soft aluminum surface into an (almost) hard-as-diamond surface that can withstand sandstorms and saltwater. In this blog post, I will share everything you need to know about hard anodizing. You will learn about the properties of hard coat, the sealing process, when you should seal as well as what questions you need to ask your anodizer.
Type II Anodizing vs. Type III Anodizing
The main purpose of anodizing is to form a thick and dense oxide layer with high wear and corrosion resistance on the rather soft aluminum. Type II anodizing is the most often used process to achieve this protective anodic layer. However, some product applications require an even thicker oxide layer – one that consists of more aluminum oxide and often is above 25 µm (1 mil). This is when hard anodizing or Type III anodizing comes into play.
On a structural level, hard coat anodizing is denser. A dense oxide layer is an oxide layer with narrow pores and very thick cell walls.

The figures show the differences in the structure of Type II Anodizing compared to Type III Anodizing (hard anodizing). The anodized layer is seen from the top and down into the porous hexagonal structure. The structure of the porous aluminum oxide layer is highly ordered.
What are the properties of hard anodized coating?
Apart from the high corrosion resistance of the oxide layer, the hard anodized oxide layer has also other valuable properties, for example, low friction and non-stick surface. But let’s look at some concrete numbers to quantify the properties of hard coat:
- Corrosion resistance: The hard anodized coating can withstand 3000 hours in a Neutral Salt Spray testing (NSS). In comparison, Type II anodizing only needs to pass 1000 hours in the NSS test.
- Hardness: The hard anodic coating has a hardness of more than 500 Vickers Hardness (HV) compared to tooling stainless steel with 950 HV. However, we are talking about a very thin hard coat layer on a very soft aluminum body. Read more about how to define the hardness of hard anodized aluminum.
- Wear resistance: Hard coating with 450 HV has the same wear resistance as tooling stainless steel with 950 HV even though the latter has almost twice the HV. The aluminum copper alloys (the 2000 series) with 2% or higher copper content have a lower wear resistance than all other alloys.
- Dielectric: 50 µm (= 2 mils) hard anodized coating will fail around 1.5-2.0 kV, sometimes higher.
- High-temperature resistance: The hard coat withstands 2000°C for a short period of time.
- Adhesion for chemicals and dye: Because of the pore structure, any chemicals will stay well on the hard coat layer without flaking off – even with high mechanical wear (e.g. a dentist drill). The hard coat can also be dyed, although it is difficult because the hard anodized layer has narrow pores and dye often consists of big dye pigments. Plus, the formed hard anodizing layer has a color of its own, ranging from dark grey (aluminum-silicon alloys) or brown to silvery aluminum (6000 series) appearance depending on the alloy. A darker hard coat is usually dyed black while a lighter hard coat can be dyed with any color.
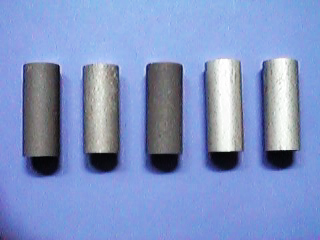
Does hard coat anodizing need sealing?
Hard coatings are usually unsealed to maintain a high wear resistance. Yet, they can be conventionally sealed or impregnated with different materials such as Teflon, waxes, and silicone. If you choose to seal the hard coat anyway, you have to consider that the wear resistance will decrease by 20 to 50% depending on the sealing process used.
However, if corrosion resistance is the most important property of the surface, sealing will enhance this property. The sealing will normally be in hot water or dichromate, which increases the corrosion resistance remarkably.
The MIL-PRF-8625 standard divides Type III into two classes regarding sealing:
- Class 1 shall be unsealed to avoid a decrease in wear and abrasion resistance
- Class 2 shall be sealed to improve corrosion resistance and is here permitted to have a reduced abrasion resistance.
How to create a hard anodizing layer?
Even though it is the anodizer’s job to hard anodize your aluminum product, it doesn’t hurt to understand the basics of this process. Of course, you first need an understanding of how the anodizing process works in general.
For hard anodizing, it is important to use higher current density so that the coating has to be formed by current-controlled processes, not voltage-controlled. Further, using electrolytes with low oxide dissolving power at low electrolyte temperature ensures a limited amount of oxide dissolution. By varying the process parameters, the characteristics of the hard coat can be “tuned” to meet specific design requirements.
What alloys can you use for hard anodizing?
To achieve homogenous and smooth anodic layers, you need to know what alloy you will use and remember to talk with your anodizer ahead of the final decision. Because structural deviations in the hard coating can be related to microstructural features in the aluminum alloy. The best results for hard anodizing can be seen on low alloyed aluminum with less than 5% copper and less than 8% silicon.
What should you ask your anodizer about hard anodized aluminum?
Whenever you work with an anodizer, you should have your own checklist to ensure you get the anodizing results you want and need for your product. After all, you will sell it to your clients, so you want to make sure you consistently get high-quality results. For that you should understand your requirements:
- Properties and expectations
- Ask for a Standard Operation Procedure (SOP) or procedure documents outlining the process sequence
- Ask for the latest tests according to industry standards or your standard
I also recommend taking a tour at your anodizer’s plant or even auditing the facility. Here is what you need to watch out for:
- Cleanliness
- Cooling capacity
- Rectifier voltage range
- Logging of process values and results
- Lab and testing facility
If you still have questions about hard anodizing or anodizing your aluminum products, you can always hire me as your go-to consultant. I have more than 25 years of industry experience and have worked with hundreds of anodizers AND companies working with aluminum products.
I also recommend you download my checklist for anyone working with anodized products. This checklist helps you to get exactly the anodized parts you want for your product. Simply fill out the form and receive the checklist.