For constructors and architects, aluminum corrosion is one of the biggest problems. Let’s say you helped to design or plan a beautiful façade with anodized aluminum window frames. A big part of your job is to also make sure that this façade will stay beautiful for decades to come by choosing the right materials – that is why you have chosen anodized window frames. But a few months later, your customer discovers white powdery patches on the window frames. Oh no, the aluminum corroded! How could this happen? And how can you prevent it next time?
What is aluminum corrosion?
Unlike steel, aluminum won’t continue to corrode as steel does, but the process is similar: the corrosion compromises the aluminum surface. There are two main reasons for corrosion:
- the type and aggressiveness of the environment
- the chemical and metallurgical structure of the aluminum
If your building is next to the Atlantic Ocean, the salt from the ocean in the air constitutes an aggressive environment. Corrosion can happen in weak spots in the oxide film.
However, local corrosion can only be found when aluminum is passive, covered by the oxide layer. A passive aluminum surface is in the pH range of 4 – 9. The passive layer could be the naturally formed aluminum oxide layer or the anodic aluminum oxide formed by anodizing.
Even though aluminum oxide formed naturally or by anodizing has a high corrosion resistance there is still a possibility to experience corrosion. The three most common types of aluminum corrosion in buildings are:
- Pitting Corrosion,
- Crevice Corrosion,
- and Galvanic Corrosion
Pitting corrosion
Pitting Corrosion is the removal of metal at localized sites on the anodized surface, resulting in the development of cavities. For pitting to occur an electrolyte must be present (high humidity can also act as an electrolyte). The weakness in the oxide around the intermetallic particles will cause a spot with two different potentials, corresponding to the pure aluminum oxide (cathode) and the intermetallic phase (active = anode). This leads to the destabilization of the oxide protecting the matrix around the particle and thereby initiating corrosion in the form of a pit. Pitting corrosion can also happen on painted aluminum surfaces due to a weak spot in the paint but here the corrosion often shows as filiform corrosion.
Crevice corrosion
Crevice corrosion occurs in the presence of a crevice formed between two aluminum surfaces – could be a gap in a corner of a window. Localized corrosion in the form of pits or etch patches may occur. An important variable in crevice corrosion is the width of the crevice opening. The aluminum-copper alloys corrode many times faster than the aluminum-magnesium alloy when crevice corrosion has started. The reason is that the aluminum-magnesium alloy has higher corrosion resistance.
Galvanic corrosion
Galvanic corrosion is due to electrical contact with a more noble metal or a non-metallic conductor in a conductive environment. The galvanic corrosion is very dependent on the cathode reaction. The efficiency of this reaction will determine the corrosion rate. Galvanic corrosion happens most often when aluminum alloys are joined to steel or copper and exposed to a wet saline environment.
What architects, constructors, and engineers need to know about aluminum corrosion
Architects will probably see all three forms of corrosion, but galvanic corrosion will be the biggest issue for the architect when mounting aluminum fronts to a steel frame with the wrong steel bolts. This could cause structural safety problems whereas pitting corrosion and crevice corrosion often are seen as more decorative problems.
Constructors will often see pitting corrosion on screen doors and crevice corrosion on corners of window frames. The reason for the latter is that the profiles are anodized in long lengths and then cut, leaving the cut ends of the profiles unprotected. These unprotected ends will together with humidity form a superb environment for crevice corrosion.
This photo shows a severe attack by crevice corrosion on electrolytic colored, anodized aluminum frame. The owner has tried to stop the corrosion attack by applying silicone but that will make the corrosion attack even worse.
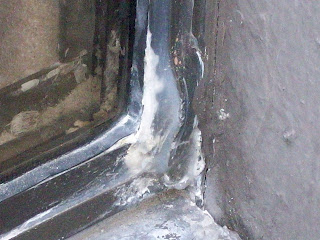
Engineers must keep all three corrosion mechanisms in mind when using aluminum in all kinds of applications – especially when considering in which environment the application will be used and what kind of alloys are specified.
How can you prevent aluminum corrosion?
Anodizing is already the solution to aluminum corrosion. However, if the anodic layer is not flawless, corrosion will happen in the weak spots. How can you ensure a flawless anodizing finish that will not corrode?
The key is to secure a good uniform oxide layer by avoiding any spots where water or chemicals could be enclosed. Also, you need to be wary about connecting the aluminum with different materials as this makes the aluminum prone to galvanic corrosion.
This is by no means an easy task. As a consultant, I have worked with many constructors and engineers in the building and façade industry. If you need help, you can contact me for consultation here.
Are you working with anodized materials?
Then grab our free checklist with 8 things to agree on with your anodizer to avoid mistakes and disappointments!