This blog post is not for the faint-hearted. We all want that perfectly smooth anodizing surface.
Unfortunately, things can go horribly, horribly wrong in the anodizing process and we are left with ugly anodizing defects that no customer should ever see.
Anodizing Defect #1: Burning
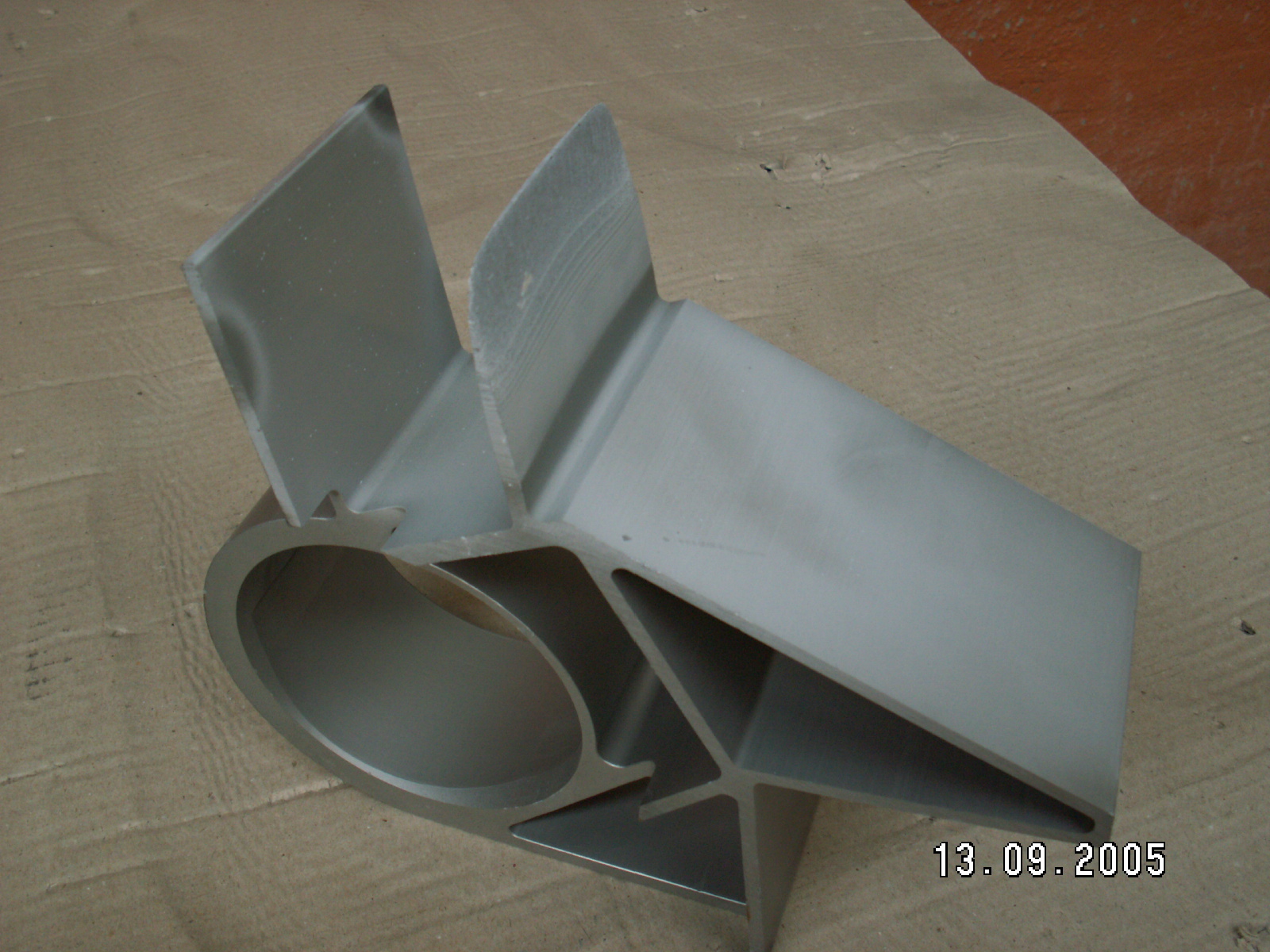
Burning is a defect that is most likely seen in Hard Anodizing (Type III) but also happening in Type II anodizing. It’s typically because of too much current running in a specific area – often thin exposed ones. The reason for this uneven flow of current is often due to an inappropriate racking of the aluminum parts. Leading to un-stable and inconsistent contact between the rack and the aluminum part creating an uneven flow of the current over the total of the rack.
Anodizing Defect #2: Fingerprints
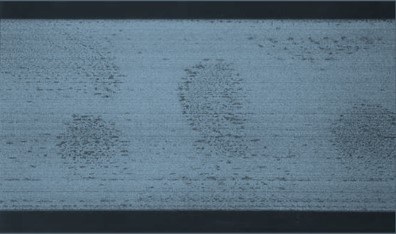
Nice fingerprint. At least if you are a detective looking for a suspect…
Not so much if you are an Anodizer looking for happy customers :-/
These fingerprints often arise when not using white cotton gloves to protect the very sensitive aluminum surface before anodizing. Leading to a corrosion attack created by the acidity of hand sweat.
Anodizing Defect #3: Staining
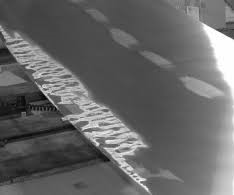
The staining seen here is from the etching tank, but staining can happen in many of the anodizing process steps from degreasing to sealing. Staining can also occur during the anodized aluminum product’s life when it comes in contact with acidic or alkaline solutions, for example during construction.
Anodizing Defect #4: Corrosion Pits
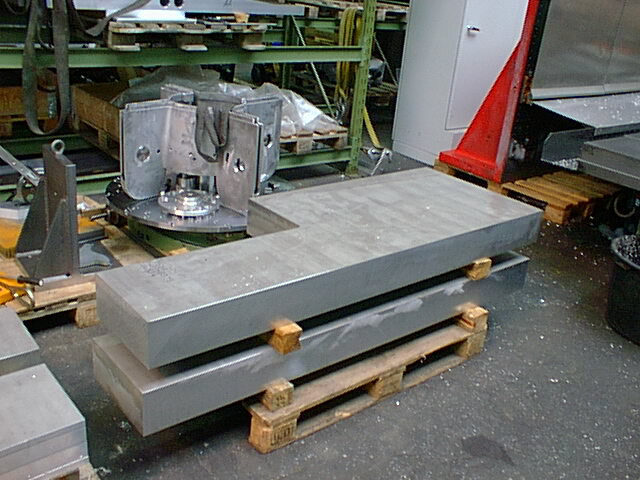
Pitting is probably the most common defect on aluminum, and origin from many places. The image shows how you should not store your bare aluminum material. Dirt, splashes of water, high humidity and several other possible contaminants can lead to a surface full of corrosion pits even before you start machining and anodizing the part.
Anodizing Defect #5: Sprangling
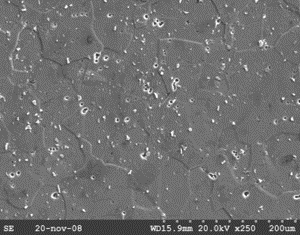
Spangling as seen in the above image happens either on zinc-containing aluminum alloys or a too high concentration of zinc in your etching tank. It’s a common defect and mainly due to etching of some of the grains – often the ones containing a high content of zinc leading to an uneven etching image of the aluminum surface.
Avoiding Anodizing Defects in Handling, Racking, and Pretreatment
What do those five anodizing defects have in common?
They are examples of how bad your Anodized Aluminum can turn out if you don’t have a procedure for handling, racking, and pretreatment in place.
With the right procedure, you will…
✓ Avoid corrosion during or because of transport, storage, unpacking, and before racking.
✓ Choose the optimal materials for racking.
✓ Create the right surface for Anodizing in the pretreatment step, so you get the best results for your Anodized Aluminum.
✓ Troubleshoot the pretreatment steps and get it done faster (without being dependent on your chemical supplier).
Are you not sure how to find the right procedure? Then check out the modules by AnodizingSchool about handling, racking, and pretreatment.
Does your company have an in-house anodizing line? Then get our free to-do list with 4 actions you can take today to increase the revenue of your anodizing line.